Online Induction >> Supplier Management System
Published 04/03/2023
Supplier Management System
- Online Supplier Management Software
What is a supplier management system and why do you need one?
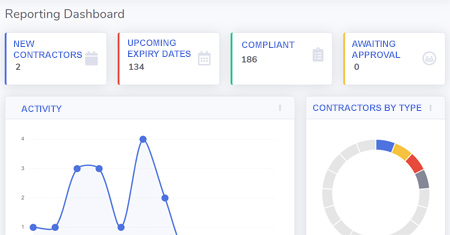
A best practice
supplier management system ensures that new and existing suppliers and contracting companies go through an extensive end to end management process covering their initial engagement and induction as a supplier through to ongoing
performance and compliance review.
A supplier management workflow first begins with an extensive
supplier prequalification,
supplier accreditation and approval process to review the safety and risk history of the supplier followed by induction of their staff, a registry of their staff, performance and risk ratings, contacts, work to be carried out, work order history, contracts, project documentation, safety reviews and supplier communications (
What is supplier management, 2024).
Some of the areas you might manage in a supplier management system
Supplier Performance Management |
Decision Making |
Licenses |
Setup Tips
|
Effective Supplier Management |
Vendor Management System |
Supplier Onboarding System
Accreditation as a supplier
The first stage is registration and accreditation of the supplier on a range of areas ranging from their provision of service, safety and performance history, financial capability, experience, insurance and evidence of training and certifications.
This workflow involves new suppliers registering online and progressing through a supplier prequalification accreditation form where they will go through an extensive supplier questionnaire.
This might be for a sole trader or a representative of a supplier company.
Once submitted, the supplier accreditation is submitted and awaits approval. There might be a number of areas to clarify or further upload such as evidence of policies, procedures and systems in place or correct copies of insurances and certifications.
Typically, the supplier accreditation questionnaire might include:
- company registration details
- services to provide
- registered business address
- preferred contacts
- accounts details
- safety history
- providing insurances
- service history
- relevent experience
- providing certifications and evidence of qualifications and evidence of training
- how to lodge invoices and company level induction
One of the most critical elements of the supplier accreditation is the risk review, safety performance history due diligence and compliance checks of suppliers.
To ensure suppliers are insured and that these insurances are valid and hold the correct type of insurance.
Supplier Prequalification
A part of the accreditation process, suppliers go through an extensive prequalification. The supplier prequalification is basically a due diligence on the suppliers safety, risk and compliance history.
This process will typically be an evidence based process where the supplier uploads evidence of their own safety systems, processes and procedures as well as evidence of safety history.
For example, prequalification questions might be:
- Does your company have documented procedures for completion of High Risk Work:
- Does your company have documented procedures for safe manual handling:
- Does your company conduct regular internal audits of its own operations:
- Do you undertake safety induction training for your employees and subcontractors:
- In the last 5 years have you been convicted of a WHS breach or been issued with a breach notice by a WHS regulator:
- In the last 5 years have you been convicted of an environmental breach or been issued with a breach notice by the state regulator:
As part of the supplier prequalification process it's important to fully verify and authenticate all performance, compliance and safety information.
Approving the wrong supplier based on the wrong merits could have serious consequences for your organisation.
Make sure that:

Support details confirmed

Service history reviewed

Safety performance is known

Quality history has been reviewed

Staff performance evaluated

Insurance details have been verified

Safety history has been reviewed

Payment details collected and confirmed

Authorised contacts known and approved
Create Supplier Management Workflow Journeys
One of the best ways to manage suppliers is with custom workflow journeys. Truly wow your suppliers with the ultimate engagement workflows, nudges and create custom workflow journeys for them to go through. Ranging from notifications, milestones and nudges based on certain activities and actions achieved through to prompts that ensure the supplier is prepared for their job activity in the workplace and even gathering their feedback.
Here's an example right here:
Induct all staff from a supplier
All individual staff who work for a supplier that your organisation has engaged should be inducted into your organisation.
Setup a Supplier Management Portal
With your own supplier management system portal, you can setup and manage your own custom supplier management workflows easily and efficiently. No two organisations are the same and so its critical ensure your supplier management system can suit your organisations specific workflows and requirements.
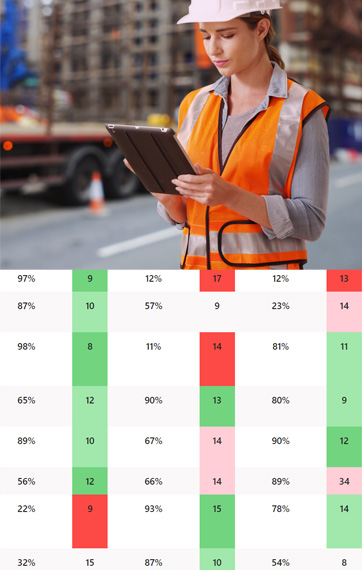
Performance review and ongoing evaluation of the supplier is a major element of supplier management once they have been engaged and start performing tasks for your organisation.
Using deep intelligence gathering technologies such as our modern supplier management software, you can discover, identify and classify all aspects and concern areas around the performance of suppliers.

New suppliers go to the link and self register

You get a notification when the registration has been successful and is awaiting approval

Easily manage pending approvals

Final registry of compliant suppliers and contractors
Manage work orders, purchase orders and other supplier management options
Once all your suppliers are using a supplier management portal, you can link in uploading purchase orders, invoices, communications, notifications, training and even work requests into a centralised supplier accreditation area.
It can be split up into a supplier request form, prequalification process and then supplier management tools as part of their ongoing business and ongoing compliance.
See how our supplier accreditation system can work for your organisations needs by looking at the online demo
Supplier Risk Ratings and risk Profile
On an ongoing basic, suppliers should be rated on their level of risk in relation to their work being conducted and their performance as a supplier and their subcontractors. Rate their risk level, categorise them as a company and their individual staff by high, medium and low.
Try our supplier management software
For a full end to end supplier management platform, try our supplier management software and customise your supplier workflows.