Online Induction >> Contractor Safety Management
Published 25/05/2024
Contractor Safety Training: Best Setup and Tips
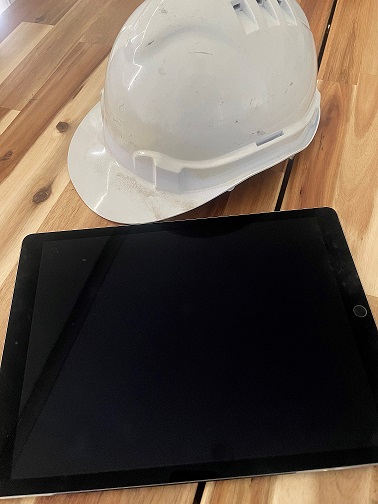
When developing contractor safety training programs, it's crucial to cover a wide range of topics to ensure comprehensive and effective preparation. A thorough understanding of occupational hazards, emergency response procedures, and safety protocols is essential for contractors working in various environments. Additionally, addressing topics such as hazard communication, personal protective equipment (PPE) usage, and job-specific safety requirements can significantly enhance the overall safety culture within an organization. By incorporating these critical topics into contractor safety training, companies can prioritize the well-being of their workforce while promoting a proactive approach to risk management.
Preparing contractors for the incidents they will face while on the job is a way of preventing workplace accidents from occurring. OSHA directs companies to train their employees and provide them with training manuals before they are allowed to work. Apart from manuals, videos demonstrating safety measures are also used. For better understanding and consultation, employees need to be trained in groups, either physically or remote.
This commonly forms part of your
contractor management system and consists of a
contractor induction. You may also train contractors around
permit to work, the
contractor prequalification process and the process around your
contractor sign in system.
View Contractor Safety Templates, Forms and Examples
What topics include in your Contractor Safety Training?
Incorporating relevant topics into contractor safety training programs is essential for fostering a culture of safety within organizations. Topics such as fall protection, electrical safety, and equipment operation are vital components of comprehensive training initiatives designed to mitigate workplace risks. Furthermore, providing instruction on hazard identification, incident reporting procedures, and regulatory compliance standards equips contractors with the knowledge and skills necessary to navigate potential safety challenges effectively. By integrating these diverse topics into their training curriculum, companies demonstrate their commitment to safeguarding the well-being of their workforce and ensuring compliance with industry-specific regulations.
Some of these areas might be covered as part of your
safety induction.
1. Equipment
When the contractors are informed about the equipment during training, they understand the type of workforce to hire and the people who can operate the machines.
2. Safety Policies
Every employer has unique safety policies which must be adhered to by contractors. The safety training should allow a section for teaching the safety policies implemented by the company and others that OSHA directs.
3. Tests
Training has a corresponding test that evaluates the understanding of safety measures. An automated safety training tests for every training session, while manual training has several tests initiated after an agreed time.
4. Training library
Training libraries store training materials for future reference and for workers to refer to when necessary. An automated library is designed as a system that stores online training materials like videos and short notes.
5. Emergency handling
The contractor is new to the company and unfamiliar with the environment. When employers hire contractors, they need to include emergency handling in the training so that the contractor knows where to get first aid support, what to do in case of fire, and the nearest medical facility where the contractor can get assistance for critical health complications, etc.
Benefits of contractor safety training
Effective contractor safety training should encompass a broad spectrum of topics to address the diverse hazards encountered in various work environments. From fire prevention and control to ergonomics and workstation design considerations, comprehensive training programs empower contractors with the knowledge needed to identify potential risks and take proactive measures to mitigate them effectively. Moreover, emphasizing the importance of maintaining a safe work environment through proper housekeeping practices and regular equipment inspections contributes to enhancing overall workplace safety standards. By including these essential topics in their contractor safety training initiatives, organizations can proactively promote a culture of vigilance and responsibility toward occupational health and safety.
- Saves time
The contractor goes through the training and understands the work environment. Before the training is administered, the contractor lacks knowledge about the company and slowly switches from one activity to the other. When the contractor has gone through the training, they connect activities easily.
- Knowledge of hazards prior to the job
The contractor is physiologically prepared for the misfortunes they may encounter while on duty. After a thorough discussion with the employer, the contractor understands the hazards associated with the job better.
- The contractor negotiates with the employer about compensation.
When contractor employees get injured while on duty, their contractor employer may have the responsibility of paying hospital bills and compensating them. The safety training gives the contractor an opportunity the degree of hazards to be exposed while working and the insurances in place.
- Understanding documentation
This is where the contractor is made aware of documentation requirements such as completing a
job safety analysis or
safe work method statement.
Self-insurance for workers compensation
Some employers wish to self-insure for workers' compensation, but some conditions must be met for eligibility. An employer is eligible for self-insurance when the following conditions are met; must be in operation for more than three years, provide proof of updated worker's compensation coverage, provide a certified financial statement for the last three years, and a copy of the safety program.
However, jurisdiction differs depending on the area. Federal laws differ from state guidelines, with the former requiring businesses to hold unemployment, insurance for the disabled, and workers' compensation, while the latter has more federal laws.
Techniques for managing workers compensation
6. Setting workplace safety standards.
A safe work environment keeps injuries and incidents low, thus saving compensation premiums. The only way to establish standards is by ensuring all employees comply with OSHA standards to minimize the risks exposed to workers.
7. Act after an injury
Compensation cost is controlled by attending to injured workers immediately after the incident. The safety team should be alert to respond to any incident and collect information to help the worker get assistance with immediate effect.
8. Keep an eye on claims fraud.
Dishonesty employees can take advantage of giving false information about an incident to get compensation. Some claims of fraud include; exaggerated accidents, injuries that occurred outside the workplace, and claims that did not cause injury to the employee.
9. Return to work plan
Return to work cancels the compensation to the claim. As an employer, be wise to advise your employees to take action to recover quickly to return to work. To entice them, you can promise salary increments and other benefits to avoid compensation.
Staying informed helps predict what may happen in the future and plan accordingly. When contractors are informed about misfortunes they may face, they plan before the job and negotiate with the employer about compensation plans.
Try setting up your own contractor safety management system